倉庫移転で気を付けなければいけないことは、準備不足です。倉庫の設計や移転計画の不足又は不備により「移転の目的が達成できない」「移転後に上手く運用できない」など、作業効率が悪化することも十分にあり得ます。
なぜ倉庫移転する際に準備が重要であるか、倉庫移転を成功させる手順を解説します。ぜひ計画的な移転業務を実行するために参考にしてください。
SCM/3PL/物流のお悩みを解決したい方へ

プロレド・パートナーズでは、現状把握から施策の立案・実行まで一貫したサポートが可能となります。SCM改善について皆様からのご相談をお待ちしております。
物流倉庫の移転を検討するタイミングと理由
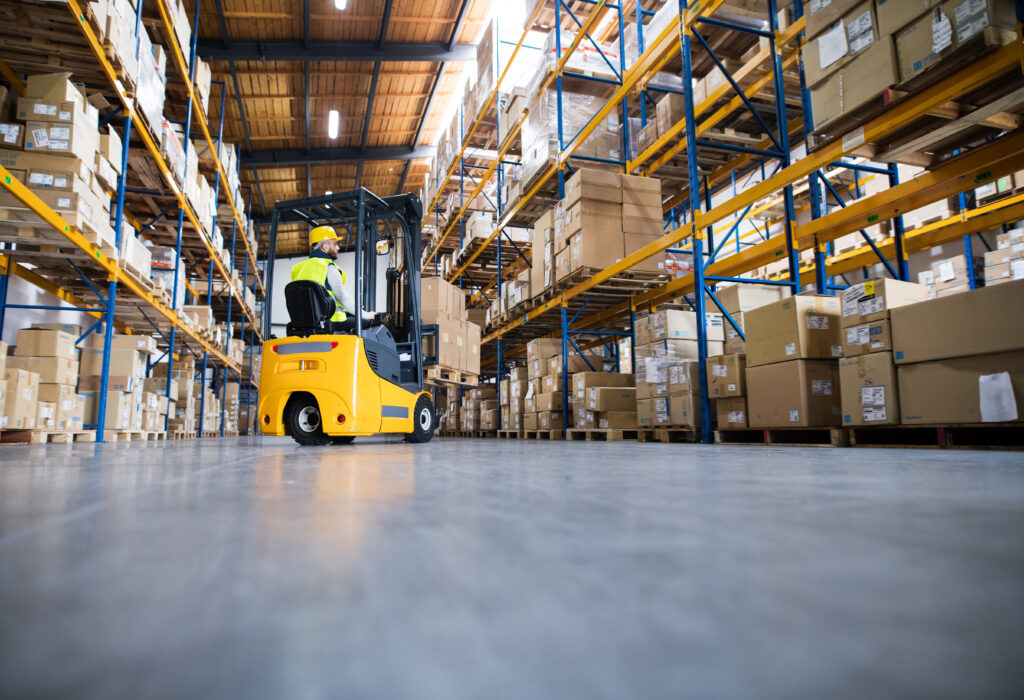
取扱量が増えて在庫の保管スペースや作業スペースが十分に確保できなくなった時が倉庫移転を検討するタイミングのひとつです。 今後事業をさらに拡大していく際に作業効率の低下や在庫保管場所の不足問題は事業の大きな障害となることが予想されます。
以下3点のいずれかに当てはまる場合は物流倉庫の移転を検討しましょう。
1.キャパシティの不足
事業拡大などにより作業や保管スペースのキャパシティが不足している場合は、移転を検討しましょう。
具体的には、以下のような状況です。
- 在庫が保管スペースから溢れ通路や作業スペースに保管されている
- 入出荷量が増えて、一日に何度も作業中の商品の移動が発生している
2.倉庫配置が最適ではない
倉庫配置の最適化の観点から現状の倉庫立地が有効かどうかの検討も非常に重要です。
以下のような状況に当てはまっていないかを確認しましょう。
- 立地周辺の交通網が変化し、出荷期限に影響が発生している
- 配送リードタイムや配送コストが増加している
- 拠点が増加し、在庫数量も増加している
倉庫配置の最適化はコストやサービスレベルの適正化につながります。事業のトレンドは常に変化を続けていますので、定期的に倉庫配置の見直しを行いましょう。
3.物流会社の値上げや品質低下
長年取引の続いている物流会社へ倉庫を委託している場合、物流会社側の方針変更や担当者の変更により、倉庫運営の値上げ要請を受け、入出荷作業の品質が低下してしまうことがあります。
具体的には以下のような状況です。
- 最低賃金を上回るパーセンテージで作業料金の値上げ要請を受けた
- 誤出荷の発生率が上昇した
- 受注オーダーを出荷期限までに出荷できなくなった
上記のようなことが起こっている場合は、倉庫の移転を伴う物流会社の変更により改善が見込めるでしょう。
倉庫移転におけるリスク
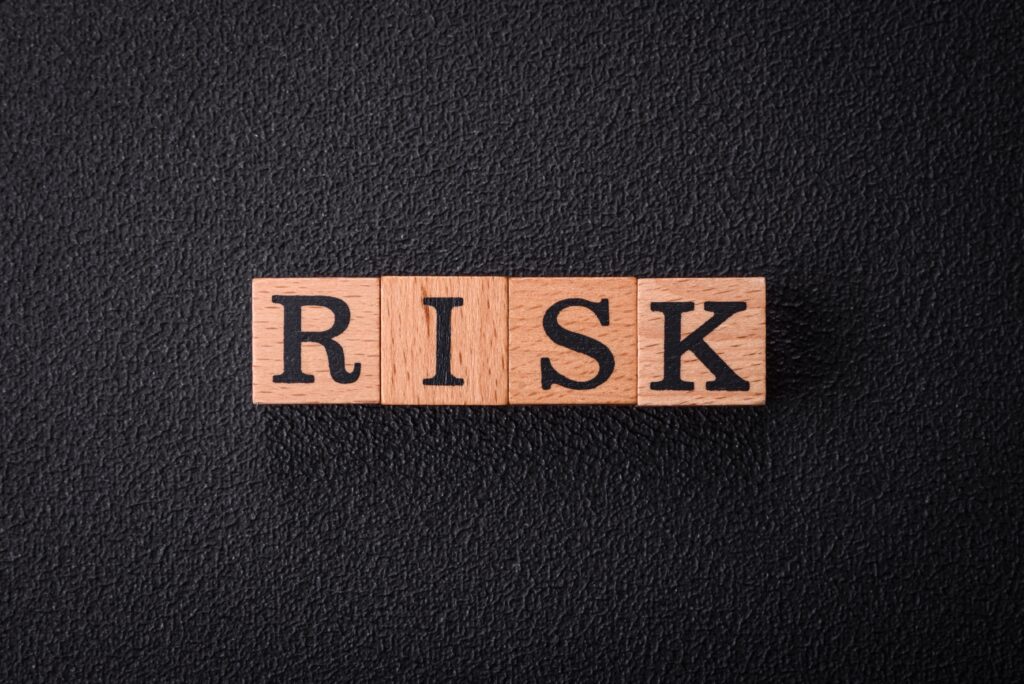
また、倉庫移転は3つの大きなリスクを抱えています。
1つでもリスクが事象化すると倉庫移転を成功させることができません。倉庫移転に潜むリスクをみていきましょう。
1.立上げ遅延
新拠点での稼働開始日までに移転が終わらない場合、追加費用が発生し出荷が出来ないことによる機会損失が発生します。
2.想定のキャパシティが実現できない
物流倉庫の保管設計が適切でないと、必要な在庫を保管できない可能性が高くなります。
また、作業設計が曖昧な場合、1日で終えなければならない作業を終えられなかったり、出荷できなかったりと倉庫内に在庫が残ることも考えられます。
3.想定コストを上回る
計画を綿密に立てていない場合、移転費用の見積りに漏れがあり、移転後の生産性が低く作業料金が計画を上回ることが考えられます。
また、旧倉庫における費用も明確にしておく必要があります。具体的には、不動在庫や備品等の廃棄費用・原状回復費用(床の補修等の工事費用)・解約金等があります。
倉庫移転におけるリスクを最小化するためには
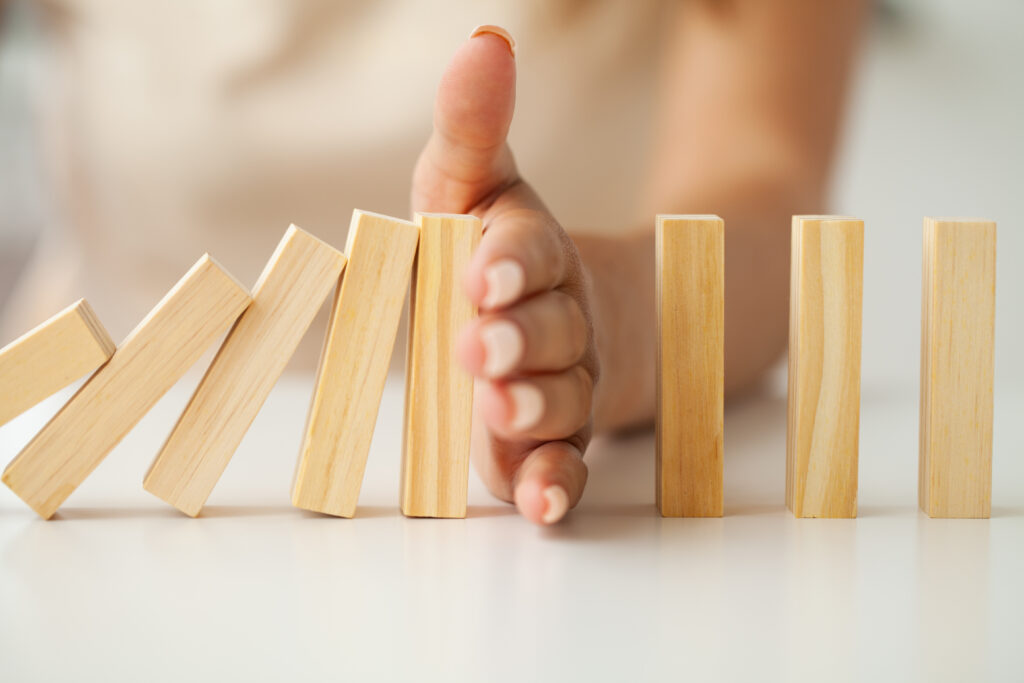
上記の3つのリスクを回避することは物流倉庫移転を成功させるためのカギとなります。
それでは、実際の計画を立てる際にどこに気を付けて計画を立てていくとよいか見ていきましょう。
倉庫設計
倉庫設計では、作業や保管レイアウト、システム、などオペレーション全体に対しての設計を行います。
新倉庫は既存倉庫とどういった点が異なるかの相違点や新倉庫の目標値などを明確にしておき、担当者間で新倉庫に関する共通認識にしておくことが重要になります。
後ほど、倉庫設計について詳しく説明いたします。
プロジェクト・マネジメント(計画と実行)
一般的に移転作業は、最短でも3ヶ月はかかると言われています。移転完了の1年〜1年半前から計画すれば、スケジュールに余裕をもって移転を進められます。
現倉庫・移転先と、それぞれで予想される作業期間から逆算してスケジュールを決定しましょう。
①スケジュール確定/車両の手配
移転の詳細なタイムスケジュールを確定させましょう。移転計画を詳細にスケジューリングすることで、工事が遅延した際に追加費用の支払いが生じたり、発送業務遅延による売上低下等のリスクを防げたりします。
現倉庫での最終出荷日、そこから搬出作業にかかる時間、移転先にはトラックで何時に到着か、荷物が全て届いたら移転先は何日で出荷できる状態にするかなど、各項目に対して細かく計画を立てておきましょう。
大規模な移転を行う場合は、商品の移動計画も重要となります。移転期間中ずっと出荷を停止することはできませんので、出荷を止める期間をいかに短縮できるかが重要なポイントとなります。
②搬出・搬入
- 搬出時
現倉庫での最終出荷が終了し、棚卸を実施して理論在庫と実際の在庫数の差異がないか確認したら棚卸結果を反映した移転全商品の商品コード、数量の一覧データを移転先へ送付します。
また、梱包ルールが守れているか、自社資産が残っていないかを確認しておきましょう。棚卸をすることで、どの時点で差異が生じたか確認が取りやすくなり探す手間を省けるため、必ず搬出時と搬入後に行います。
- 搬入時
搬入時の商品の扱いや商品マスタに無い商品、移転予定データに無い商品などイレギュラー時の確認をする際は、現場に出向いて確実に自分の目で確認しましょう。
③プロジェクトリソースの確保
プロジェクトが円滑に進むよう、下記の内容を事前によく確認しましょう。
重要なポイントはバッファ(余剰)の考え方です。
複数か月に及ぶ移転計画のバッファは集中的に管理(一か所にまとめ)し、期間の短縮をめざしますが、数日以内で完了する移転日では、全ての工程やリソースに十分なバッファを設定し、絶対に遅延が発生しない体制を構築します。
実施すべき内容 | 考えられるリスク |
余裕を持ったスケジュール作成 | 遅延した場合、稼働開始が遅れる |
十分な人員確保 | イレギュラーに対応できず作業遅延 |
専門的な梱包方法 | 搬入~搬出の過程で破損する |
休憩時間の確保 | ・作業の遅れを取り戻そうと休憩なしで働き続けると、かえって作業効率が低下 ・注意力散漫で労災の可能性あり |
作業者への十分な説明 | ・情報源が多いと指示がうまく伝わらない |
倉庫の設計について詳しく

ここからは移転先の倉庫が決まっている前提で話を進めていきます。移転先決定後から必要な計画や設計についてみていきましょう。
概要設計
新倉庫は既存倉庫とどういった点が異なるかの相違点や新倉庫の目標値などを明確にしておき、担当者間で新倉庫に関する共通認識にしておくことが重要です。
特にキャパシティやコストについて、荷主企業と物流企業間の考えをしっかりと擦り合わせておきましょう。
概要設計の段階では倉庫のDX(自動化・システム化)に関する方針も検討します。
レイアウト設計
倉庫全体のスペースを確認して、できるだけデッドスペースが生まれないようにレイアウトを決めます。
デッドスペースをなくすためには「平面ロス」だけでなく、「高さロス」が生じないように意識しましょう。
- 平面ロス:スペースが余っていて商品が置かれていない
- 高さロス:倉庫の高さを上手く活用できていない
また各工程から次の工程に進むとき、作業場所が遠いと移動時間が無駄になります。
作業をする場所も考慮しながら動線を確認し、効率がよい最適なレイアウトを設計しましょう。動線を決めるときには以下の2つから、新倉庫に最適な動線を考えると効率的なレイアウト設計ができるでしょう。
①I字型動線
入荷から出荷までの作業スペースを順番にまっすぐ並べるレイアウトです。
建物の端と端にそれぞれ入荷・出荷用の扉がある倉庫に向いています。
ただし、作業場所や通路が狭い倉庫で複数の作業をすると、作業員同士が邪魔になり作業効率が下がる可能性があるため注意が必要です。
②U字型動線
入荷と出荷の場所を同じにする、U字を書くようなレイアウトで作業場所や通路が狭い倉庫でも作業効率を確保できます。
商品の配置の決め方は出入りが激しいものから考えます。重要度の高い商品は中央通路寄りに配置し、重要度が低い商品は台車が通れないような通路幅の狭い通路に配置するなどの工夫が必要です。
可能な限り無駄のない動きでピッキングできるレイアウトを作成しましょう。
オペレーション設計
物流におけるオペレーションとは、「入荷→検品→入庫→保管→ピッキング→梱包→出荷」の一連の流れを言います。 そのため、倉庫オペレーションを把握するためには、各業務工程を正しく理解しておくことが重要です。
そこでここからは、倉庫オペレーションで重要な各業務の特徴について解説します。
①入荷
入荷とは、発注した商品が物流倉庫に入ってくる工程を指します。入荷した商品や荷物は、数量や製品自体に問題がないか確認する「検品」という作業がとても重要です。
入荷はオペレーション中で最初のプロセスなので、入荷でミスが起きると出荷ミスや返品などのトラブルが多発する恐れがあります。 入荷検品は工数をかければかけるほど、精度は上がりますがコストとリードタイムが増加します。必要な検品レベルの定義が必要となります。
②保管
入荷して検品が済んだ商品は、保管プロセスに入ります。保管とは、商品を出荷まで決められた場所においておく工程で、この際に重要なのがロケーション管理です。
ロケーション管理とは、商品の保管場所を適切に管理することをいいます。ロケーション管理をすることで、商品を探し回る手間を省けます。主に出荷頻度などで商品群を作り、適切に配置することでより効率的なロケーション管理を実現させる工夫が重要です。
出荷頻度の高い商品を出入り口に近い場所へ置いたり、取りやすい高さに配置したりすることで、効率を上げることが期待できます。
③ピッキング
ピッキングとは、出荷指示された商品を取り出す作業を指します。ピッキング作業は正確かつスピーディな作業が求められる一方で、作業ミスが起こりやすいプロセスの1つです。
ピッキングミスは誤出荷という重大な事案につながる可能性もあるので、効率の良い作業内容とミスが起こりにくいピッキング方法を検討します。
また、マニュアル作成と作業者への周知、チェック体制を確立し、正確な業務ができる環境作りが必要です。
⑤梱包・出荷
梱包、出荷のプロセスが、物流倉庫内の最終工程です。 保管していた商品は受注後に梱包プロセスに入り、商品に適した資材(緩衝材など含む)を使用して梱包されます。
梱包はその手順を考えることも重要ですが、ピッキングや検品の工程とのバランスを考慮することが重要です。
システム設計
ここまでオペレーション設計を考えましたが、システムを導入することで検討したオペレーションをより確実に構築することができます。
ここから、より効率的に運用していくために有用なシステムを見ていきましょう。
以下の3つのシステムを紹介します。
①倉庫管理システム(WMS)
倉庫管理システム(WMS)とは入出荷・在庫・棚卸管理、帳票・ラベル発行機能、返品管理などの倉庫運営に関わるほとんどのシステムを指しています。
システム上でリアルタイムに管理可能なので、人為的ミスの削減や業務の標準化を実現できるほか、ロケーション管理の効率化も可能です。また、商品を探す手間も省けます。
WMSについては以下コラムで詳しく解説しています。
②ピッキングシステム
ピッキングシステムにはさまざまな種類があり、バーコードやRFIDタグ、デジタル表示器を用いた方法、音声を活用した方法などがあります。
現在は用途に応じて多様化しており、ピッキングミスを抑制できるほかにも従来のピッキング作業をより効率化することが可能です。
加えてピッキング業務自体が標準化されるため、属人的なデメリットを改善できます。
要員設計
マテハン機器の導入を進めながら人員構成も考えます。
人員構成とは、オペレーションに必要な事務と作業者の数を選定し、各チームの構成やリーダー数、社員とパートタイマーのバランスを検討することです。総人員のうち正社員の比率が10~15%以内に収まっていれば問題ありません。
20%を超えていると、そのセンターは高コストなセンターの可能性があります。正社員は固定人件費にカウントされ、売上が下がってもかかる費用なので利益を減少させます。
まとめ
物流倉庫移転の際のスケジュール管理や移転後の人や機械の運用方法について解説しました。 倉庫移転におけるリスクも把握したうえで、プロジェクトも設計・計画・実行が重要になります。倉庫移転は簡単にできるものではなく、たくさんのコストがかかるため失敗できません。
プロレド・パートナーズでは倉庫移転にかかるコストマネジメントにおける専門家も在籍しておりますので、倉庫移転を検討している方はぜひお気軽にご相談ください。
SCM/3PL/物流のお悩みを解決したい方へ

プロレド・パートナーズでは、現状把握から施策の立案・実行まで一貫したサポートが可能となります。SCM改善について皆様からのご相談をお待ちしております。