倉庫スペースを有効活用するには、保管効率を上げることが重要です。保管効率が上がれば、より多くの商品を在庫でき、適正な倉庫レイアウトは入出荷作業を円滑にします。しかし、倉庫の広さや設備、商品の形状や種類などによって対策が異なるため、改善に踏み出せない方も多いのではないでしょうか。
今回は、倉庫の保管効率を高める方法を解説します。現状把握から改善までの手順も取り上げるので、ぜひ参考にしてください。
SCM/3PL/物流のお悩みを解決したい方へ

プロレド・パートナーズでは、現状把握から施策の立案・実行まで一貫したサポートが可能となります。SCM改善について皆様からのご相談をお待ちしております。
倉庫の保管方法
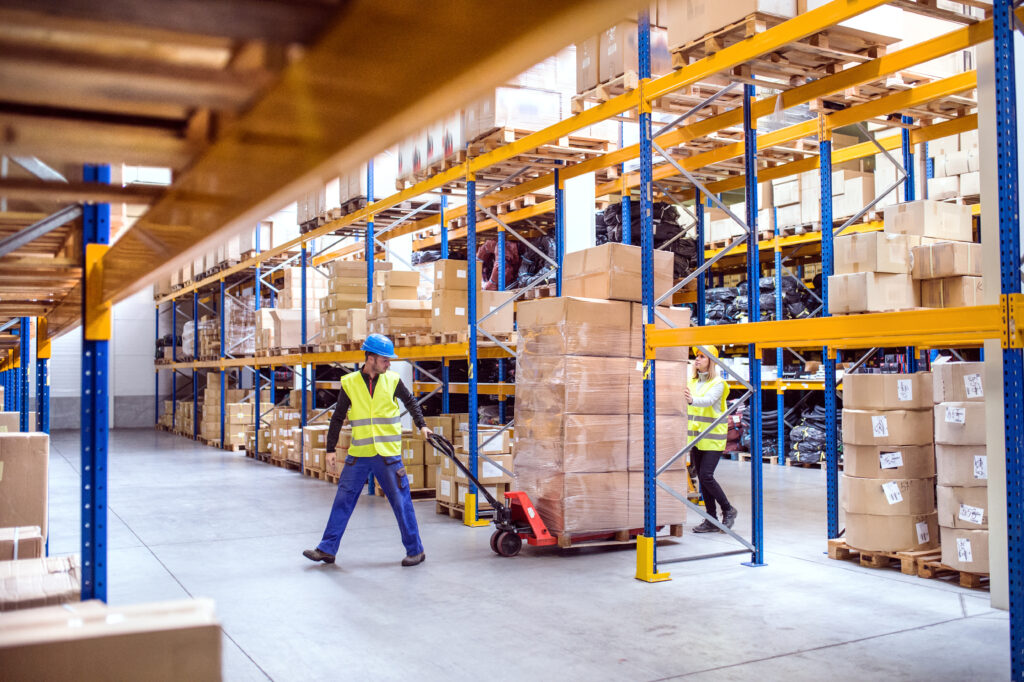
倉庫の保管効率を高めるには、保管方法の特徴を正しく理解して、スペースロスを見直す必要があります。以下の項目で、自社の商品に合う保管棚やラックを見ていきましょう。
物理的な保管方法の違い
まずは、物理的な保管方法の違いを解説します。
代表的には以下の7種類です。
(1)平置き
床に商品を直接置いて保管する方法です。
ラックなどを使用しないため安価に導入でき、置き方に縛られることもありません。
(2)重量ラック(パレットラック)
パレットに商品を乗せたまま保管できるラックを使用した保管方法です。収納力が高く、商品に合わせて棚の高さを調節することも可能。1段あたり積載荷重500kgを超える商品も保管できます。
(3)軽量ラック
商品に合わせて分解や組み立てができるラックを使用した保管方法です。
比較的小さく、軽い商品の保管に適しています。
棚板の高さを変更できるため、山欠けロスの削減に効果的です。
(4)積層ラック(簡易中二階)
倉庫の天井空間を有効活用した中二階式のラックを使用した保管方法です。
床面積が2倍になるため、商品を無駄なく保管できます。
しかし、建築床や建築物と見なされると建築確認申請が必要になるため、導入までに多くの時間と費用がかかります。
(5)高層ラック
通常のラックを高く積み上げた、大きな本棚のようなラックを使用した保管方法です。
スペースロスになりやすい倉庫上部を最大限活用できます。
(6)移動ラック
床に設置したレールに沿って棚を動かせるラックを使用した保管方法です。固定されたラックに比べ、省スペースで商品を収納できます。ラックを横に移動させれば、作業スペースの確保も可能です。
(7)自動倉庫システム
コンピューターで管理する倉庫のことで、クレーンやベルトコンベアを使用して、商品の出し入れをおこないます。作業が自動化されるだけでなく、スペースを効率的に使えるようになります。
運用上の保管方法の違い
商品の保管場所を住所化して管理する方法を、「ロケーション管理」といいます。倉庫内のどこに商品があるのかを把握しやすくなるため、ピッキングや出荷作業の効率化を図れます。
ロケーション管理には3つの種類があり、倉庫内で扱う商品や管理状態に合わせて最適な方法を選ぶのが重要です。
(1)固定ロケーション
商品の種類ごとに保管場所を固定する管理方法です。
良く出る商品を出荷作業場所へ集めるなど商品の出荷特性に合わせた商品配置がしやすくなるため、ピッキングの効率化につながります。
ただし、商品ごとの保管スペースの広さと保管場所を出荷傾向に合わせて、常に変更する必要があるため、メンテナンス作業の工数が必要となります。
保管している商品数が少なく、取り扱う商品が頻繁に変わらない倉庫に適しています。
(2)フリーロケーション
商品ごとに保管場所を決めない保管方法です。空いているスペースに自由に保管できますので、スペースの有効活用につながります。無駄なくより多くの商品を保管できるのが特徴です。新しい商品が次々入荷されても、その都度倉庫のレイアウトを変更する必要はありません。
しかし、同じ種類の商品が別々の場所に保管されてしまう場合があるため、通常よりピッキングに時間がかかることもあります。ピッキング効率の悪化は倉庫管理システムのデータを活用して解消できます。フリーロケーションを検討する場合は、ピッキング効率の悪化を解消するための倉庫管理システムの導入が必須となります。
(3)ダブルトランザクション
ダブルトランザクションは、在庫をピッキング用とストック用の2種類のエリアに分けて保管する方法です。
ピッキングエリアでは出荷効率を高めるために固定ロケーションを、一方のストックエリアでは、商品を無駄なく保管するためにフリーロケーションを採用するのが一般的です。
しかし、ストックエリアからピッキングエリアへ商品を補充するため追加の作業工数が必要となります。倉庫スペースが広く、ピッキング時の歩行距離が長い倉庫において、ピッキングエリアを狭めることによる動線短縮を目的として採用されています。
倉庫の保管効率の把握方法とは
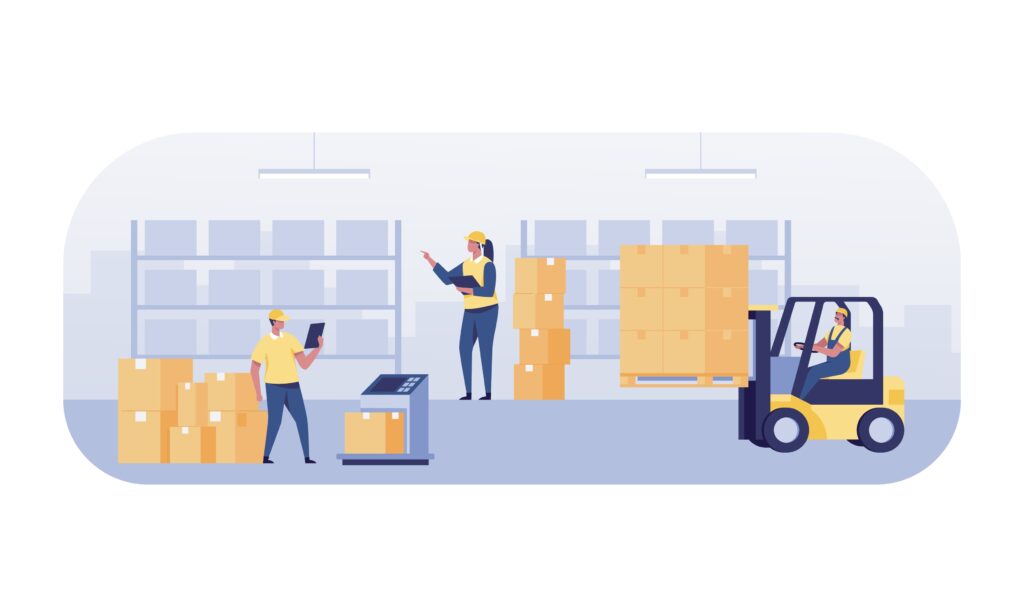
保管効率を高めるには、現状を把握することが大切です。
以下の手順に沿って、現時点でどの程度のスペースロスが発生しているかを確認しましょう。
- 理論的な倉庫スペースを算出
- 理論値と実際のスペースロスを分析
順番に解説します。
1.理論的な倉庫スペースを算出
スペースロスを把握するためには、まず理論的な倉庫スペースを算出する必要があります。消費されるスペースは保管方法や機材によって異なるため、それぞれに適した計算式を使用しましょう。
ここでは、以下の条件のラックをもとに、理論的な倉庫スペースを計算します。
- 奥行:1.2m
- 幅:2.6m
- 通路幅:3.3m
- 段積み:3個
- 保管パレット数:6個
この場合、1ラック分の倉庫スペースは(1.2+3.3÷2)×2.6=7.41㎡になります。
通路幅を2で割っているのは、ラック同士が背中合わせで並んでいる状態を想定しているからです。1パレット分の倉庫スペースは、7.41㎡÷6=1.235㎡になります。
2.理論値と実際のスペースロスを分析
理論的な倉庫スペースがわかったら、実際に倉庫で利用しているスペースと比較します。比較の結果、実際のスペースが理論的なスペースより多く使われている場合は、スペースロスが生じている可能性が高いです。
なお、スペースロスには種類があり、以下の3つに分類されます。
(1)平面ロス
倉庫の広さに対して、商品が置かれていない場所があることによって発生するスペースロスです。平面のデッドスペースが多かったり、通路幅を必要以上に取りすぎていたりするケースも該当します。
(2)高さロス
空間を立体的に活用できていないことが原因で生じます。
倉庫の上部にまだ利用できる空間が空いている場合が多く見受けられます。
(3)山欠けロス
保管している商品の間に、無駄な隙間が空いているケースです。ラックの大きさや段数にあわせて商品を配置できていないことが主な原因です。
これら3つのうち、どのスペースロスが発生しているのかを把握して改善することで、倉庫の保管効率を高められるでしょう。次の項目で具体的な改善方法を解説します。
倉庫の保管効率を上げる方法
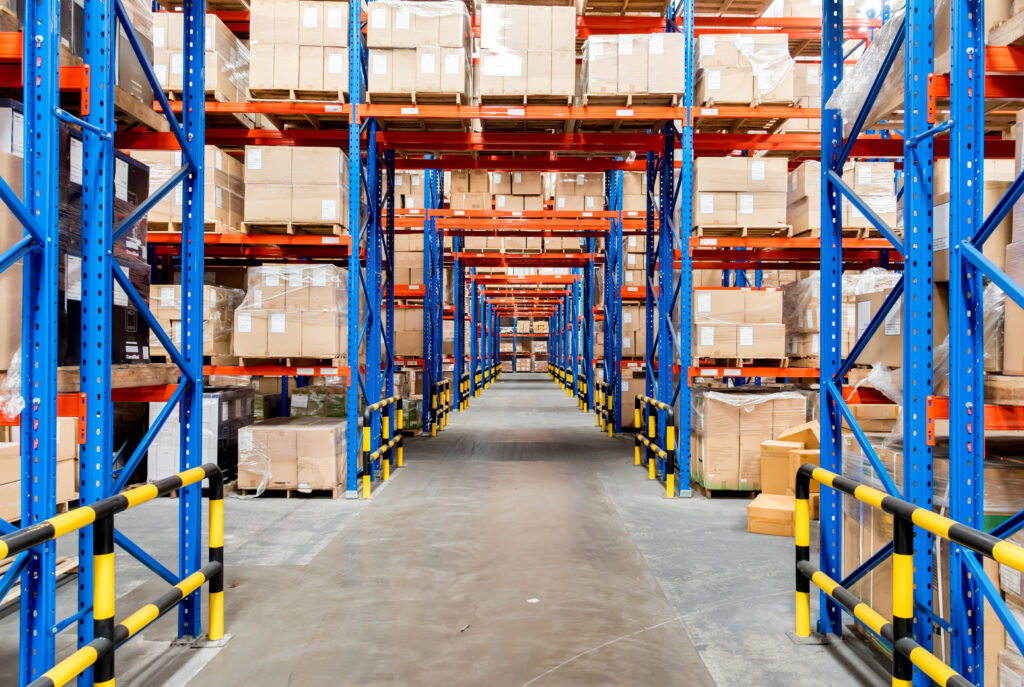
倉庫の保管効率を高めるには、余剰スペースをいかに削減するかが鍵となります。
ここからは、スペースロスの種類別に具体的な改善策を解説します。
平面ロス改善
通路幅や保管場所以外の作業スペース(商品の仮置き場など)が広すぎると平面ロスが生じやすくなります。
倉庫のレイアウトや設置数を見直したり、出荷頻度ごとに商品の保管場所を分けたりして、倉庫全体の広さに対して商品の保管面積の占有率が高くなるように意識する必要があるでしょう。
高さロス改善
ラックの種類を見直して、上部の空間を最大限活用しましょう。具体的には、積層ラック(簡易中二階)や高層ラックを活用して、通路を確保したまま上部に商品を積み上げていく方法が有効です。
山欠けロス改善
商品と商品の間に発生するスペースを削減する方法が効果的です。ラックの長さに合わせて、荷姿が似た商品を収納しましょう。隙間が生まれやすい小さな商品は、仕切り板を活用して、保管スペースを細分化しましょう。また、保管数量に合わせて保管方法を選定することでも改善が可能です。
まとめ
倉庫の保管効率を高めるためには、理論的な倉庫スペースと実際の消費スペースを比較して、現状を把握することが重要です。
理論値と実値に大きく差が生じる場合は、ラックや商品の保管場所を見直して、スペースロスの削減に取り組みましょう。 プロレド・パートナーズでは、現状把握から施策の立案・実行まで、幅広くサポートします。倉庫の保管効率向上に取り組みたいが、何から手を付けてよいかわからない方は、ぜひ弊社までご相談ください。
SCM/3PL/物流のお悩みを解決したい方へ

プロレド・パートナーズでは、現状把握から施策の立案・実行まで一貫したサポートが可能となります。SCM改善について皆様からのご相談をお待ちしております。